Todd Swinderman, emeritus president of Martin Engineering, costs itself to design security in a system as just the security of security and shows innovations that improve security that can be retrofitted in almost every Belt funding system.
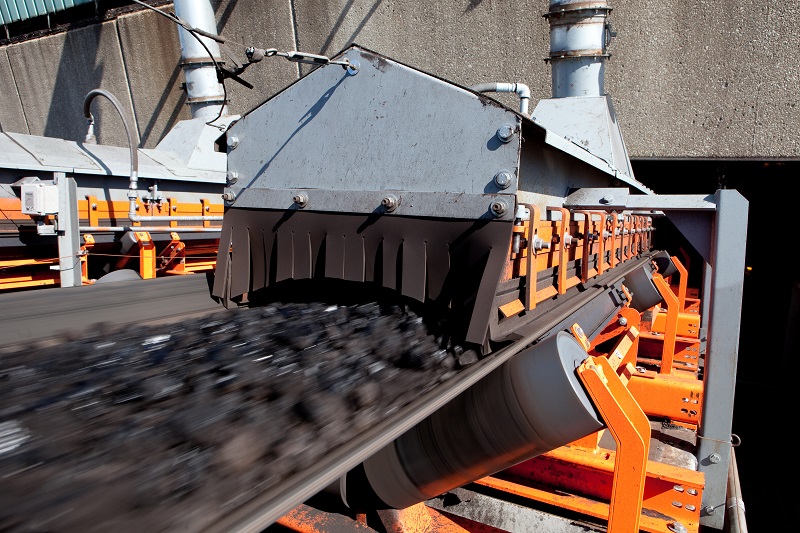
A properly designed sponsor controls emissions for improved security and simpler maintenance. All pictures © Martin Engineering 2025
Sponsors are among the fastest and potentially dangerous freight transport systems in a BULK handling company. Although their security and performance are of crucial importance for the success of the operation, the effects of their contribution to overall efficiency are often not recognized by management and employees alike. The operational basics of Belt promotion systems are too often a mystery to employees who have little understanding of the installed hardware and the performance of the components.
The knowledge gap is understandable. The attention of the staff at a Bulk handling process focuses on logistical and planning concerns. The “care and feeding” of belt conveyors – ie the adaptation, maintenance and troubleshooting – make a big difference to safety and performance, but is usually outside the operator's specialist knowledge. It is not the case that you are not interested in sponsors, but the ongoing maintenance and service of these systems is often usurpated or removed for other problems.
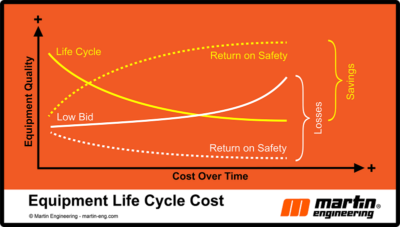
The return of the better design and quality is realized over the longer lifespan and safety of the system.
Process and life cycle costs with low BID
Although the guideline of companies is generally not expressly stated, the process with low BID is usually an implicit rule that is integrated into the culture of a company. It encourages the bidders to follow a belt promotion methodology based on following the maximum load on the conveyor belt and the minimum compliance with the regulations with the lowest price materials, components and manufacturing processes.
Maximizing the freight volume and minimizing the system system usually means selecting the closest realizable belt and working at a highly possible speed. This leaves a low mistake for errors and in many cases leads to slide cubes, excessive spilling and a reduced lifespan of the device.
When companies buy the price, the advantages are often of short duration and the costs increase over time, which ultimately leads to losses. In contrast, the services are generally continued for purchases based on the lowest long -term costs (life cycle costs), and the costs are lower, which leads to net savings over time.
Funding system design hierarchy
In order to maximize production, designers and engineers are asked to approach the project with a certain set of priorities. Instead of fulfilling the minimum compliance standards, the funding system based on the global best practices should exceed all the requirements for the code that exceeds security and regulatory requirements. By designing the system to minimize the risk and the flight and accumulation of refugee material, the workplace becomes safer and the equipment is easier to wait.
The life cycle calculation should adhere to all component decisions. Note the specifications for project components that indicate “specific manufacturer name/or the same”. Vague -written “or same” specifications are available for competitive reasons and enable the contractors to buy a price without adequate consideration of construction or performance. The purchase of life cycle costs or in engineer approved or equal purchase of future use of components of problem solving in the fundamental configuration of the sponsor offers improved security and access without increasing the structural steel requirements or significantly increasing the total price. It also increases the possibility of lighter system upgrades in the future. The ability to absorb future capacity increases can also be included in the original design, expand options and reduce future change costs.
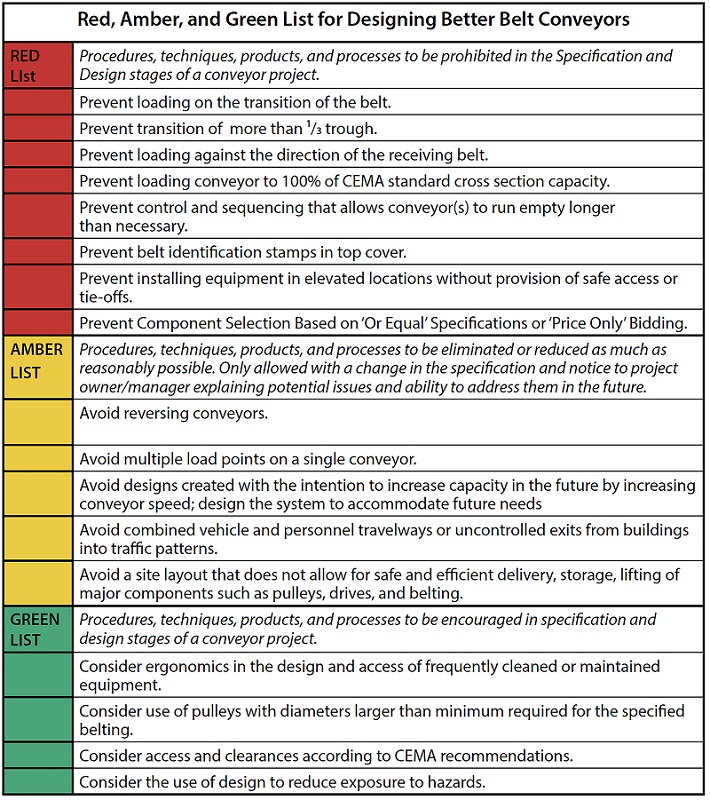
Instead of fulfilling the minimum compliance standards, conveyor systems should exceed the code that exceeds security and regulatory requirements.
Designing supporters upgrades for security
The managers are continuous pressure to increase production in order to meet customer demand. However, the standards continue to tighten, since the government's regulatory authorities keep their strong focus on the safety of employees and drive the need for device design that are not only securely but also optimized for security (designed for security). The staff is the most important resource of an industrial company. For this reason, designers for conveyor systems integrate greater functionality in designs that improve security.
In order to reduce the dangers at the workplace, the operators set a variety of methods, from the use of personal protective equipment (PSA) to installation of the latest and safest device designs. When examining the safety of a system, improving efficiency and reduction in risk can be achieved by using a hierarchy of control methods to relieve dangers. The consensus among security experts is that the most effective way to reduce risks is to eliminate the risk of design. As a rule, this requires greater initial capital investment than short -term corrections, but provides cheaper and permanent results.
Examples of leaving through design are longer, higher and densely sealed chargers to spill dust and spilling or high-performance prime and secondary cleaners to minimize transport. By using hazard identification and risk assessment methods at the beginning of the construction process, engineers can create the safest and most efficient system for space, budget and application. These designs alleviate several dangers in the workplace, minimizing cleaning and maintenance, reducing unscheduled downtime and extending the lifespan of the belt and the system itself.
Experienced engineers often recommend that operators keep an external company to examine the system requirements and to design new devices for historical problems and specific requirements of the application. An outdoor eye can generally observe potential dangers that can be overlooked by employees who experience every day.
Before the draft phase, designers should set the goals of reducing injuries and exposure to dangers (dust, spilling, etc.) in order to increase the availability and productivity of the sponsors and to receive more effective approaches to ongoing operating and maintenance challenges. Designs should be future-oriented that exceed compliance standards and improve the ability of the operators to include future upgrades inexpensively and easily by a modular approach.
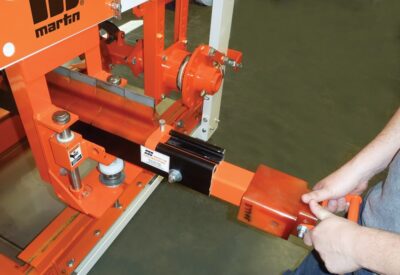
This radiated belt cleaner is constructed in such a way that it is safely accessed and replaced by a single worker.
Combine security and productivity
In order to meet the requirements for greater security and improved production, some manufacturers have introduced device constructions that not only constructs for safer operation and maintenance, but also shorten the maintenance time. One example is a new family of high-performance conveyor belt cleaners, which are designed in such a way that the blade cassette can be pulled away from the belt for safe access and replaced by a single worker.
The same interpreter technology was used to influence the construction of cradle designs. The systems are constructed in such a way that the operators can safely work on the equipment without breaking the movement level. The external maintenance reduces the locked -up room entry and eliminates the maintenance of the achievement and at the same time makes it easier to replace. The result is greater security and efficiency with less downtime.
Another example is a revolutionary new belt cleaner design, which can reduce the need for bulky urethane leaves as a whole, an innovative belt cleaning system that has received the Australian Bulk handling price in the “Innovative Technology” category for its design and potential advantages. The patented design offers an extended service life, low belt clothing, significantly reduced maintenance and improved security, which ultimately supplies lower ownership costs.
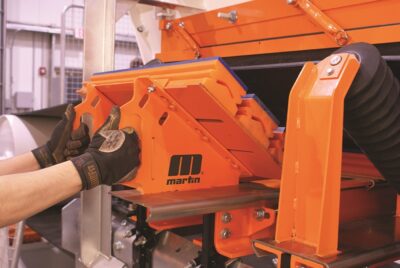
The systems mounted on the route can be waited quickly and safely without the maintenance being achieved.
In contrast to conventional belt cleaners, which are mounted in an angle to the belt, the unique cleaner diagonally is installed via the discharge disk and forms a three -dimensional curve below the discharge area that corresponds to the shape of the strap. The new approach was so effective that in many processes in many decisive secondary strap cleaners have become unnecessary and that the costs for the belt cleaning and the service period further save.
Diploma
Engineering advisor is a long-term strategy. Although the design absorbs less than 10% of the total budget of a project, the Engineering Procurement Construction Management (EPCM) services can also make up 15% of the installed costs of a main project, additional preliminary information and the use of a life cycle cost methodology for the selection and purchase of configuration components. The installation of a developed basic supporter can be achieved by promoting the use of the hierarchy of controls in the planning phase and the design hierarchy in the design phase. The system will probably meet the requirements of modern production and safety regulations with a longer operating time, less stopover and lower operating costs.
About author: R. Todd Swinderman, emeritus president of Martin Engineering, acquired his BS from the University of Illinois in 1979, whereby he joined Martin Engineering's funding from Martin Engineering and then acted as VP and General Manager, President, CEO and Chief Technology Officer. He has written dozens of articles and papers that presented at conferences and customer facilities all over the world and held more than 140 active patents. Swinderman was the president of the sponsor Equipment Manufacturers' Association (Cema), was editor of the 6th and 7th edition of Cema by Belt sponsors for Bulk materials, the design manual for Belt sponsor. It is active in several Cema committees, including the chairman of the Bulk Safety Committee and member of the ASME B20 committee for funding security, which has determined the security standards of the US funding. Swinderman withdrew from Martin Engineering to found his own engineering office that currently served as an independent consultant. |
![]() |